2013
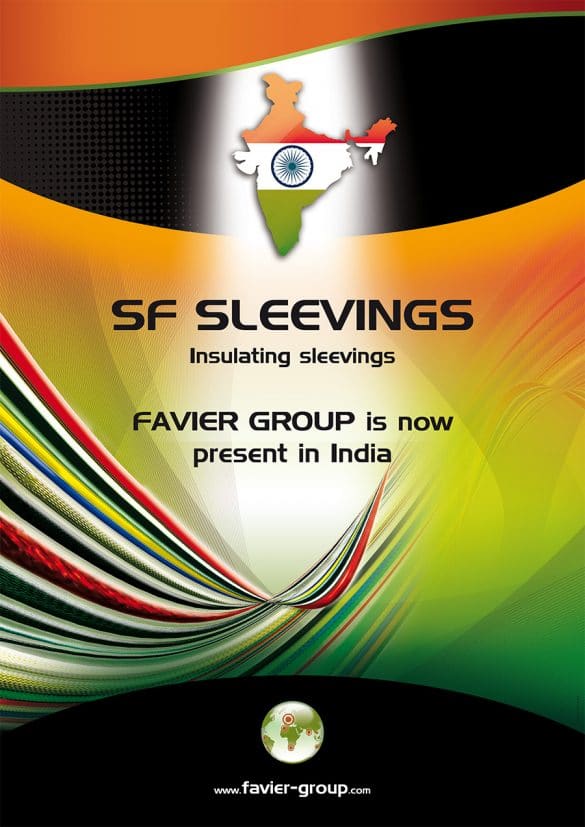
Creation of a Joint Venture in India.
2012
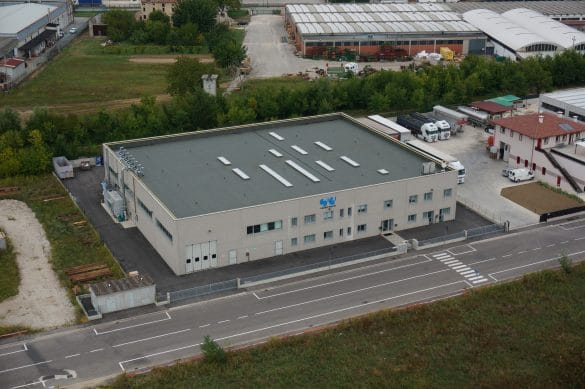
Relocation of SIGI plant in a new building.
2011
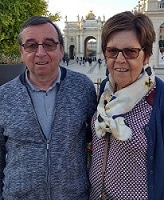
After more than 35 years in the company, including 25 years at the head, Nicole and Michel get retired and leave place to the fourth generation. Mathieu becomes the new director of FAVIER TPL.
2010
2007
2006
2005
Favier Group acquires the Italian company SIGI, with the aim of expanding its presence on the Italian market.
2004
The production plant located in Bertignat increases the area of his braiding workshops of 1500m2.
2001
Following the recruitment, three years earlier, of a Quality Anticipation and Strategic Monitoring manager, the company gets ISO 9001: 2000 certification.
2000
The company orientates a part of its operations to composite braiding, both by purchasing a machine specially designed for this type of production and by signing a partnership with a manufacturer of carbon yarn.
1994
Acquisition of ISO 9002 certification after a three-year period of bringing up to standard.
1990
1985
The company purchases its first high-speed machines.
1984
Marcel Favier gets retired and is replaced by his son Michel, whereas Jean-Claude takes over responsibility for production and quality. Nicole Favier, Michel’s wife, is in charge of the accountancy.
1974 - 1975
Jean-Claude, his second son, joins the company. He takes control of Ribeyre site and Michel of Bertignat site.
1973
Tresses et Plastiques du Livradois (TPL) is founded.
The family business is split in two: the braiding part remains in Ribeyre while the other part, which is to become the product varnishing and finishing factory, moves to Bertignat in a former convent school (see photo) where Marcel Favier went to school.
1959
Marcel Favier extends the existing buildings and buys machines.
For the requirements of the market, he goes into braiding glass yarn, still as a sub-contractor.
1955
1927
Thanks to the mill, he also has the benefit of the energy provided by the water to power the machines and to generate current to light the workshops.
He has 2,000 carriers and produces mainly flat braid, shoe laces, S-twill, brace ties, etc. that he produces as a sub-contractor.